MaintainX is a mobile-first maintenance and asset management platform built for the new industrial workforce. It empowers frontline teams to manage work orders, assets, parts inventory, and purchase orders more efficiently, reducing unexpected downtime and boosting production capacity. MaintainX leverages AI and IoT to connect asset and work data, providing real-time insights that drive proactive maintenance and operational excellence for 10K+ customers across physical asset-driven industries.
We recently sat down with Philippe Tessier, Staff Engineer at MaintainX, to learn more about what it’s like working at a cutting-edge startup that is transforming workforce productivity. Our conversation explored his career path, the challenges of engineering at a rapidly scaling business, what makes MaintainX’s engineering team stand out, and exciting developments on the company’s horizon.
Interview
What originally sparked your interest in software engineering? Can you share a bit about your career journey?
I come from a family of engineers—my father was an engineer, and so was my grandfather. Ironically, engineering was the last thing I thought I’d pursue, but when the time came to choose, I decided to give coding a try.
Once I started programming, I was instantly hooked. The endless problem-solving opportunities in software engineering drew me in, and I loved the freedom to dive deeply into various areas.
I began coding in college, which felt late compared to my peers, so I took on side projects and a part-time job to catch up and gain experience. After university, I worked with a lot of startups, drawn by their fast-paced environments and then transitioned to freelancing. Joining MaintainX felt like a natural return to that world—it’s rare to find a startup in Montreal scaling this quickly. I was particularly excited about contributing to a high-growth environment, where every decision has a meaningful impact.
What specifically drew you to MaintainX?
At the time, I was close to accepting an offer from another company, but a good friend of mine, Michael Ferris, had just left Microsoft to work at MaintainX. This intrigued me, so I reached out to see if they were hiring and they were!
After meeting the leadership team, I rejected the other offer. My conversations with MaintainX were amazing—the interview process went smoothly, and I felt more energized after each discussion. The leadership’s involvement in hiring impressed me, and it felt like the right place to build something great with people I connected with. I’m a bit of a rebel—I like to challenge ideas and act with urgency and it seemed like something they highly valued.
How would you define MaintainX’s value proposition?
MaintainX offers a solution that shifts the maintenance process in the industrial world from being reactive to preventive, and eventually prescriptive. Traditionally, technicians spend their days responding to issues as they arise—responding when something breaks. What we do is provide a framework that helps prevent those issues from happening in the first place. This includes speeding up processes and implementing comprehensive preventive maintenance plans. By doing so, we empower maintenance teams to focus on ensuring everything runs smoothly rather than constantly repairing breakdowns. Teams that use MaintainX, for example, reduce unplanned downtime by 34%. For me, that’s the biggest impact we have—helping free these teams up to invest their time into more meaningful, proactive work that improves both efficiency and job satisfaction.
What do you consider to be the most significant challenge in your day-to-day role, and how do you approach it?
The biggest challenge I face as a Staff Engineer is managing my time effectively. In the past, I could simply put in extra hours to take on initiatives or focus on improving the company culture, but at this level, time is a finite resource. The challenge is maintaining productivity at the highest level while balancing more responsibilities and initiatives.
To tackle this, I try to find better ways of working—like using AI tools to save time. It’s hard to come up with new ideas when you’re stuck in the day-to-day grind, so I share my thoughts early and see what my teammates think. If everyone’s excited, I will move forward with it. I also love supporting other people’s ideas when I see potential, teaming up to help bring them to life. Collaboration often leads to real changes that make the company and its culture better for everyone.
What makes the engineering team at MaintainX stand out? Can you share any surprises or learnings from your time here?
One of the things that stands out to me is how genuinely nice and resourceful everyone is. This might sound simple, but it’s something that sets MaintainX apart. During onboarding, new hires consistently mention how supportive and collaborative the team is. I don’t know if it’s our strict no asshole policy, but no rivalry between teams—everyone works with the best interests of the company and each other in mind.
We are also a very customer-centric engineering team—our engineers are incredibly in tune with the needs of our customers. As an example, our team recently visited a Cintas plant and it was eye-opening to see our product being used in a real environment because there’s so much as an engineer that you don’t think about. For instance, most of our users use larger fonts on their phones because they’re in a badly lit space or there’s dust everywhere. Our QA colleague observed that everyone worked with gloves on. He quickly asked for sets of the same gloves to test the app with, just so he could see if the app worked well from their perspective. It’s essential to immerse yourself in the use cases and day to day of the end user.
This level of obsession towards the end user is refreshing, especially in a technical field where it’s easy to get caught up in complex coding projects. At MaintainX, it’s always about solving real problems and improving the customer experience.
Since you joined, MaintainX has over 5x’d in headcount and been named one of Forbes’ best startup employers. How would you describe the company’s culture in three words, and could you elaborate on why?
I’ll cheat a bit, but we have an engineering value at MaintainX that encapsulates our culture: We Accept Pull Requests. This idea, drawn from open-source projects, encourages everyone to contribute, whether to the codebase or company processes. For example, when I joined, the onboarding process felt a bit rough. I was empowered to make changes right away, introducing an onboarding retrospective and improving feedback loops. This openness extends to every aspect of the company; if you have a suggestion, you’re encouraged to implement it.
That being said, the three words we use to describe the people at MaintainX are Smart Humble Optimists.
MaintainX is building the leading predictive maintenance software for the modern industrial workforce. How does the engineering team leverage AI to ensure they are at the forefront of digital transformation?
We already leverage many use cases for AI within our product. Our key use case has been anomaly detection, where it identifies potential issues with assets or machines by analyzing new metrics in real time. We also use AI to simplify workflows—technicians can input a few instructions, and the AI generates comprehensive procedures for specific machines. Voice-to-text functionality is another AI-driven feature, allowing technicians to record comments in noisy or challenging environments without typing.
Our AI vision is evolving further with the integration of Large Language Models (LLMs). In manufacturing, knowledge is scattered—tenured technicians carry decades of experience, while Original Equipment Manufacturers (OEMs) provide thousands of pages of service manuals, often not digitized.
Imagine a technician describing an issue to the system and receiving tailored tools, parts, and a step-by-step adaptive path to fix the problem—seamlessly pulling from manuals and historical knowledge. This combination of AI and LLMs is set to transform how knowledge is accessed and applied on the frontlines, helping technicians work smarter and faster.
What career advice would you give to aspiring software engineers in startups?
First, don’t look too much at what employers are looking for—focus on your strengths. The key to becoming a great developer is repetition and putting in the time, which is only possible if you’re passionate about what you do. Find that thing you love and dive into it.
Second, startups value initiative and ownership. Take responsibility for tasks, even those outside your direct role, and demonstrate the value you bring.
Finally, remember that working at a startup is often about solving interpersonal problems. Strong communication skills and being a good culture fit are critical. Everyone needs to feel supported and able to give their best. Technical skills can be learned, but a collaborative mindset is essential to succeed in startups.
Looking ahead, how do you envision the company evolving or growing in the near future? What developments or milestones are you most excited about?
MaintainX’s growth feels inevitable—the market loves what we’re offering, and there’s so much potential to build more. Over the past year, we doubled our engineering team, and if we could double it again, we’d be able to create even more amazing things.
One recent milestone that excites me is our presence at the International Manufacturing Technology Show (IMTS), where we unveiled a new product called “Asset Connect.” This tool helps OEMs connect directly with customers, allowing them to share critical information about their assets.
We also introduced “Asset Hub,” where clients can install a full preventive maintenance package in one click. Customers can instantly access manuals, parts lists, and maintenance procedures. This will empower employees to perform preventive maintenance seamlessly, right out of the box, which I’m excited about.
To learn more about MaintainX, check out our interview with CEO Chris Turlica, the MaintainX website, and open jobs.
Related Articles
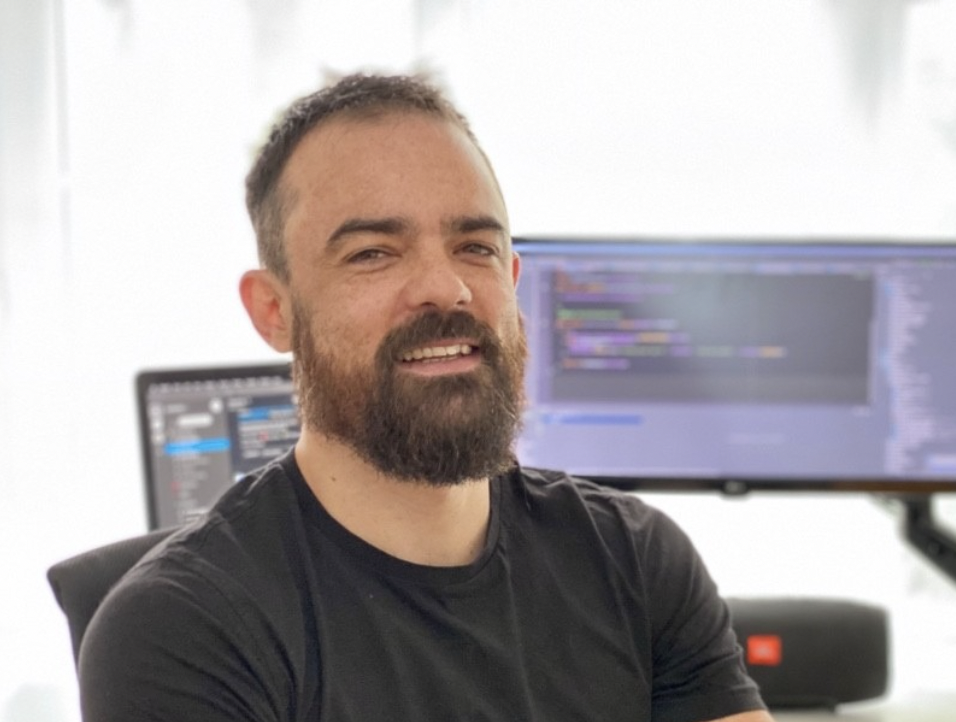
Inside Hook: A Day in the Life of Engineering Leader Nic Parry
We recently sat down with Nic Parry, a Senior Software Engineer at Hook, to explore what it's like working at…
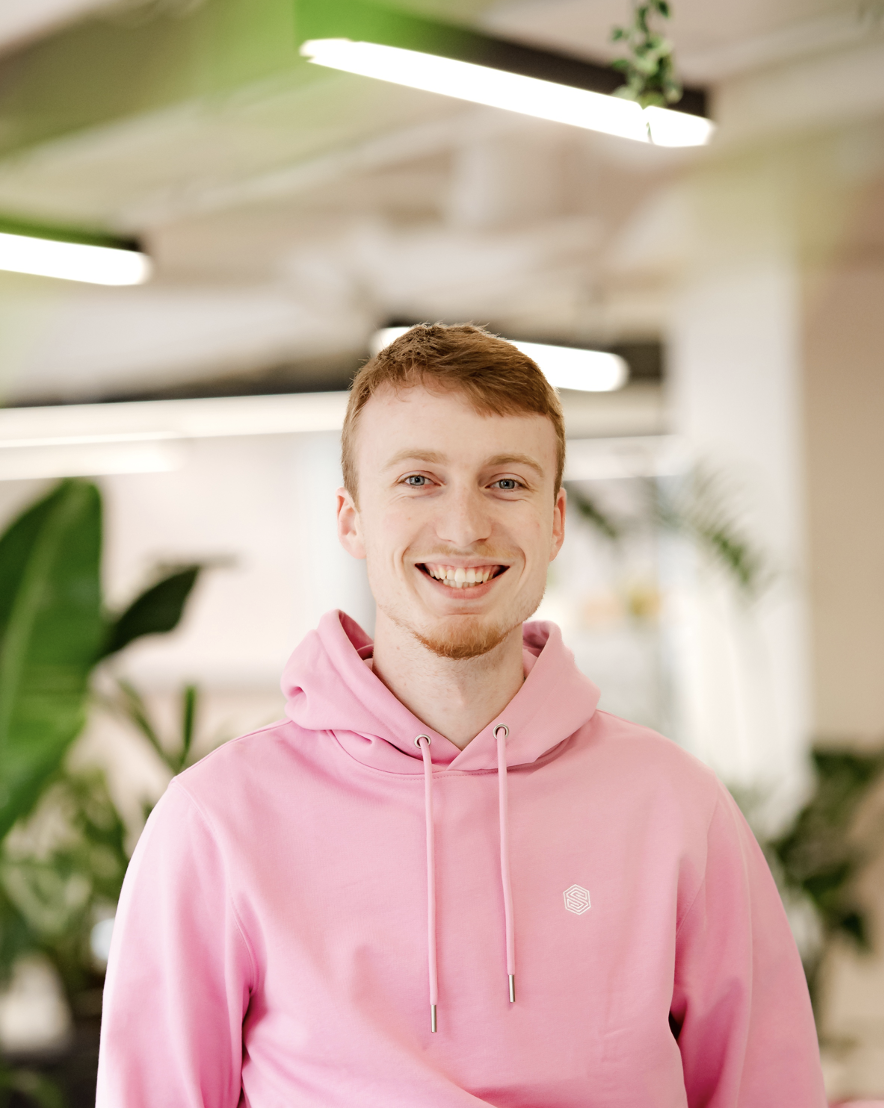
Inside SurrealDB: A Day in the Life of Software Engineer, Micha de Vries
We recently had the pleasure of sitting down with Micha de Vries, a software engineer at SurrealDB, to dive into…
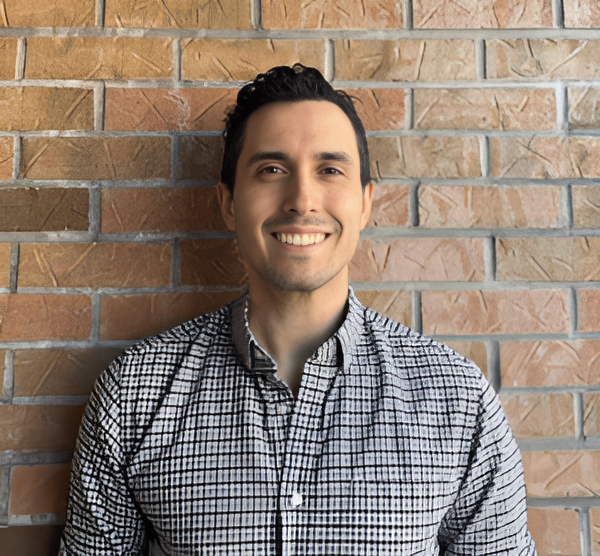
A Day in the Life at Aktos with Alvaro Atienza
Crew Capital recently sat down with Alvaro Atienza, Staff Site Reliability Engineer (SRE) at Aktos, to learn more about what…